High Precision Cutting Tool – APET Recyclable Material
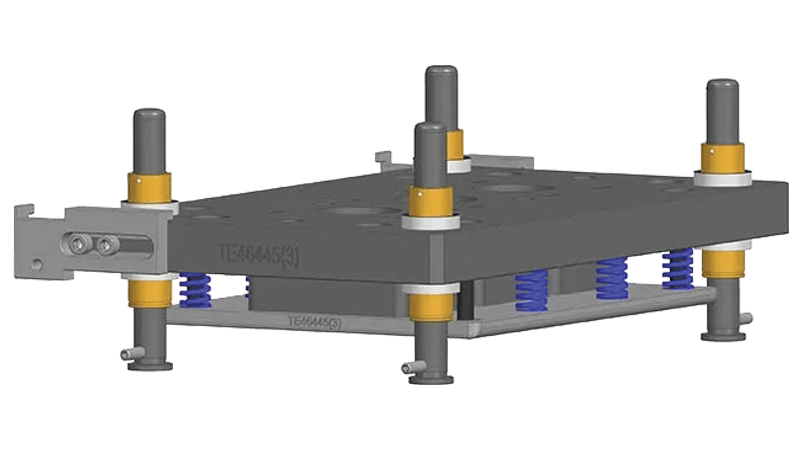
The Objective
A customers came to us asking us to supply tooling for a new blister they wanted to package. The material that was being used was APET. This is not yet common in the blister packaging industry. The reason for using APET was that unlike other common forming materials it is more easily recyclable.
From a tooling manufacturing perspective using APET for blisters provides some challenges, mainly on cutting. For materials such as PVC, when being die cut, penetration of the die through 50% of the material thickness is generally enough to get a clean, particulate free break. For APET, the die has to virtually cut through 100%.
APET material is also more damaging to standard punches and die as a greater force and strain is experienced when cutting.
The Approach
TEG first engaged with the APET material manufacturer to get all technical details on the specific material and best practices for forming and cutting of the material.
Extensive testing on the material in TEG to determine the optimum design for the new cutting tool.
The Results
A new cutting tool was manufactured with a range of improvements made in order to cut each APET material with a clean consistent cut all around with no particulates, these included;
- Ground Punch and Die to give the tightest tolerance when cutting – removing the issue of particulates
- New punch shear angle to give best results
- Extra hardened steel used for punches and die to increase life cycle of tool
- High precision cutting tool pillars, ball cages and bushings to ensure most accurate punching